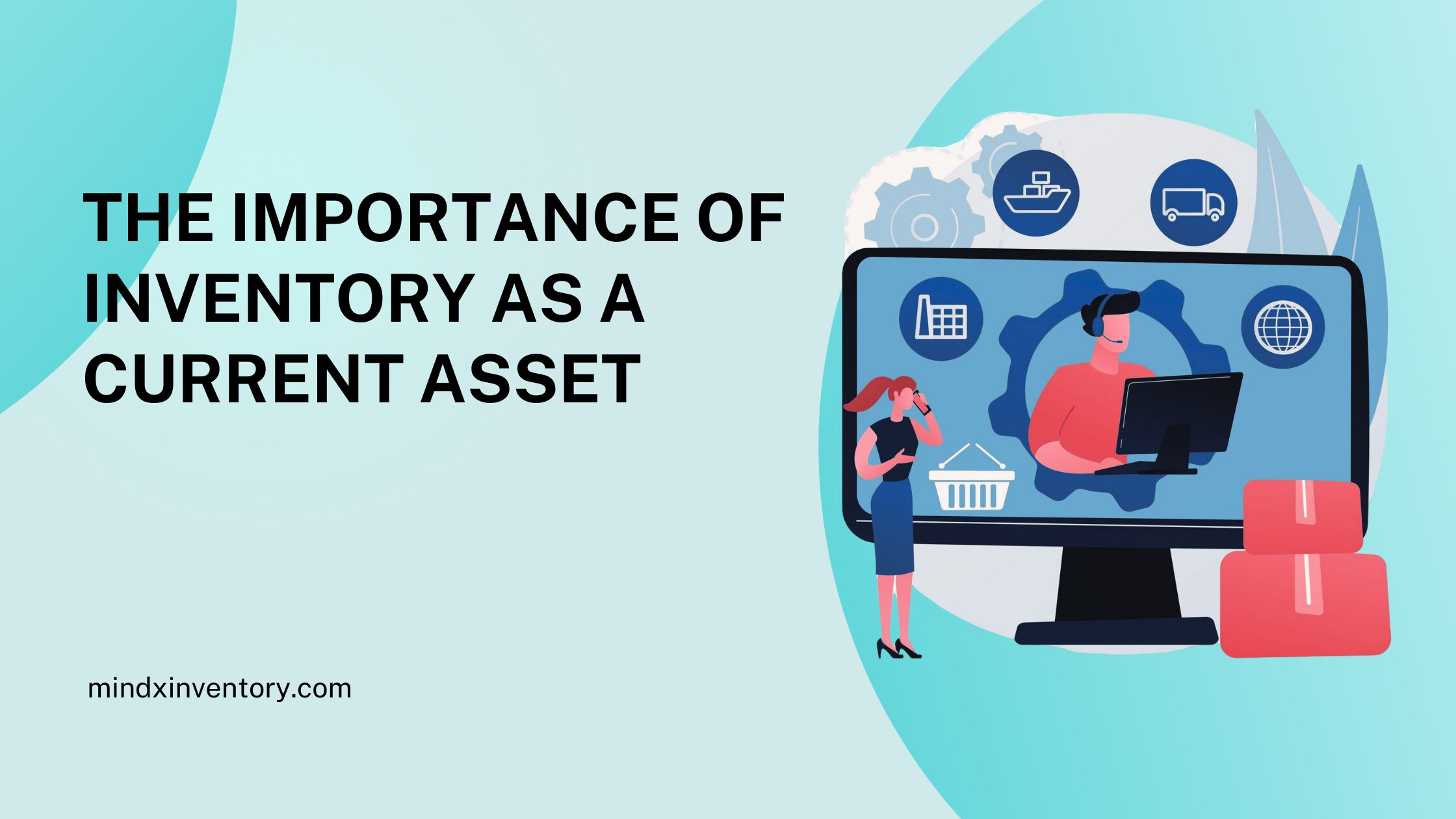
Introduction
Inventory management is a crucial aspect of any business, directly impacting cash flow, operational efficiency, and profitability. Proper inventory management not only helps in tracking and controlling inventory levels but also plays a significant role in a company’s financial health. The classification of inventory as a current asset on the balance sheet is fundamental for financial analysis and decision-making, influencing everything from liquidity ratios to cash flow management. This blog explores the nuances of inventory as a current asset, delving into its importance, management techniques, and the role of advanced solutions like Mindx Inventory in optimizing inventory processes.
What is Inventory?
Inventory refers to the goods and materials that a business holds for the ultimate purpose of resale or production. It is an essential component of the supply chain and includes various forms of goods, such as:
- Raw Materials: These are the basic inputs used in the production process, such as steel, wood, or fabric. They are the building blocks for creating finished products.
- Work-in-Progress (WIP): These are partially completed products that are still undergoing manufacturing. This category includes items that have begun the production process but are not yet ready for sale.
- Finished Goods: These are the final products that are ready for sale to customers. Finished goods are the result of production and are typically stored until they are sold to end-users.
The primary purpose of inventory is to ensure that businesses meet customer demand without interruption. By balancing stock levels effectively, businesses can avoid overstocking, which leads to excessive holding costs, and stockouts, which result in lost sales and dissatisfied customers. This balance is achieved through various strategies, methodologies, and technologies designed to enhance inventory management.
The Importance of Inventory in Business
Inventory plays a vital role in business operations, impacting production, sales, and customer satisfaction. Proper inventory management ensures that businesses can meet customer demand promptly. When inventory levels are managed effectively, businesses can maintain optimal stock levels, ensuring product availability without tying up too much capital in unsold stock.
- Operational Efficiency: Effective inventory management enhances operational efficiency. By maintaining optimal stock levels, businesses can streamline production processes, reduce downtime, and avoid excessive inventory costs. This efficiency translates into better resource utilization, improved cash flow, and increased profitability.
- Customer Satisfaction: Timely product availability is crucial for customer satisfaction. Stockouts can lead to lost sales, frustrated customers, and damage to a brand’s reputation. Conversely, proper inventory levels help foster customer loyalty and encourage repeat business, ensuring a steady stream of revenue.
- Cost Management: Effective inventory control can significantly reduce costs. By minimizing holding costs associated with excessive inventory, businesses can lower expenses related to storage, insurance, and potential obsolescence. Additionally, efficient inventory management allows businesses to allocate financial resources more effectively, supporting other areas of the business.
Is Inventory a Current Asset?
Yes, inventory is classified as a current asset on a company’s balance sheet. This classification is critical for financial analysis, as inventory is expected to be sold or used within a year. The current asset classification allows businesses to manage working capital effectively and assess liquidity.
As part of working capital, inventory influences key financial ratios such as the current ratio and quick ratio, which assess a company’s short-term financial health. Efficient inventory management ensures sufficient working capital without tying up excessive resources in unsold stock, maintaining liquidity and supporting business activities.
Understanding inventory as a current asset is crucial for investors and stakeholders, as it reflects a company’s operational efficiency and ability to generate cash flow.
Inventory Valuation Methods
Inventory valuation methods are essential for financial reporting and tax purposes. The choice of valuation method can significantly impact a company’s financial statements. Common methods include:
- First-In, First-Out (FIFO): This method assumes that the oldest inventory items are sold first. During inflationary periods, FIFO can result in higher reported profits since older, lower-cost items are matched against current revenues, reflecting a more favorable gross margin.
- Last-In, First-Out (LIFO): In contrast, LIFO assumes that the newest inventory items are sold first. This method can reduce taxable income during rising prices by matching higher-cost items with current revenues, ultimately improving cash flow.
- Weighted Average Cost: This method calculates the average cost of all inventory items available for sale. It smooths out price fluctuations over time, providing a more stable measure of inventory costs.
Each method has its advantages and disadvantages, and the choice depends on various factors, including the nature of the business, industry practices, and specific financial reporting requirements.
Inventory Management Techniques
Effective inventory management combines various techniques to ensure optimal stock levels, reduce costs, and improve overall efficiency. Key techniques include:
- Just-In-Time (JIT): This technique minimizes inventory by receiving goods only as they are needed in the production process. JIT reduces holding costs and the risks of obsolescence. However, it requires precise demand forecasting and reliable suppliers to ensure that production is not interrupted.
- Economic Order Quantity (EOQ): The EOQ model helps businesses calculate the optimal order quantity that minimizes the total cost of ordering and holding inventory. By balancing these expenses, businesses can achieve cost savings and maintain sufficient stock levels.
- ABC Analysis: This technique categorizes inventory into three groups based on their value and importance:
- ‘A’ Items: These are the most valuable and require close monitoring to avoid stockouts.
- ‘B’ Items: These have moderate value and require less frequent monitoring than ‘A’ items.
- ‘C’ Items: These are the least valuable and can be managed with minimal oversight.
By prioritizing inventory management efforts according to these categories, businesses can allocate resources more efficiently.
The Role of Technology in Inventory Management
The advent of advanced technologies has revolutionized inventory management, providing businesses with tools for real-time visibility, predictive analytics, and automation. Key technologies include:
- AI-Driven Solutions: Artificial intelligence can predict demand patterns, optimize stock levels, and automate various tasks, significantly reducing human error and improving efficiency.
- IoT Devices: The Internet of Things (IoT) allows for real-time tracking of inventory movements, enhancing transparency and accuracy in inventory management. IoT sensors can provide data on stock levels, allowing businesses to respond swiftly to changes in demand.
- ERP Systems: Enterprise Resource Planning (ERP) systems integrate inventory management with procurement, sales, and finance functions, ensuring seamless data flow across departments. This integration facilitates better decision-making and enhances operational efficiency.
Mindx Inventory exemplifies how technology can enhance inventory processes, providing features such as real-time tracking, automated reordering, and advanced analytics that optimize inventory management for greater efficiency.
Benefits of Using Mindx Inventory for Inventory Management
Mindx Inventory offers a comprehensive solution for inventory management, equipped with features that streamline processes and enhance decision-making:
- Real-Time Tracking: Mindx Inventory provides accurate, up-to-date inventory levels, enabling businesses to make informed decisions and prevent stockouts or overstocking.
- Automated Reordering: The system can automatically generate purchase orders when inventory falls below predefined thresholds, ensuring that businesses maintain optimal stock levels without manual intervention.
- Advanced Analytics: Mindx Inventory delivers insights into inventory trends, facilitating accurate demand forecasting, stock optimization, and ongoing process improvements. These insights help businesses anticipate changes in demand and adjust their inventory strategies accordingly.
By leveraging these features, businesses can reduce costs, improve efficiency, and enhance their overall inventory management strategies.
Common Inventory Management Challenges
While effective inventory management offers significant benefits, businesses often face challenges that can hinder their operations. Common challenges include:
- Demand Variability: Fluctuations in customer demand can lead to stockouts or excess inventory. Businesses must adopt accurate forecasting techniques and flexible strategies to adapt to changing market conditions.
- Supply Chain Disruptions: Delays from suppliers or transportation issues can impact inventory availability. Building strong relationships with suppliers and developing contingency plans can mitigate these risks.
- Maintaining Optimal Stock Levels: Balancing customer demand with holding costs is a constant challenge. Regular audits, accurate forecasting, and advanced systems like Mindx Inventory are essential for maintaining optimal inventory levels.
Best Practices for Inventory Management
Implementing best practices can significantly enhance inventory processes and overall business performance:
- Regular Audits: Conducting regular physical counts and reconciliations helps ensure record accuracy and uncover discrepancies that could impact financial reporting.
- Accurate Forecasting: Utilizing historical data, market trends, and advanced forecasting techniques enables businesses to predict demand more accurately and adjust inventory levels accordingly.
- Leveraging Technology: Businesses should embrace automation, real-time visibility, and actionable insights provided by AI, IoT, and ERP systems to enhance their inventory management capabilities.
By adopting these best practices, businesses can streamline their inventory management processes, reduce costs, improve decision-making, and ultimately enhance their bottom line.