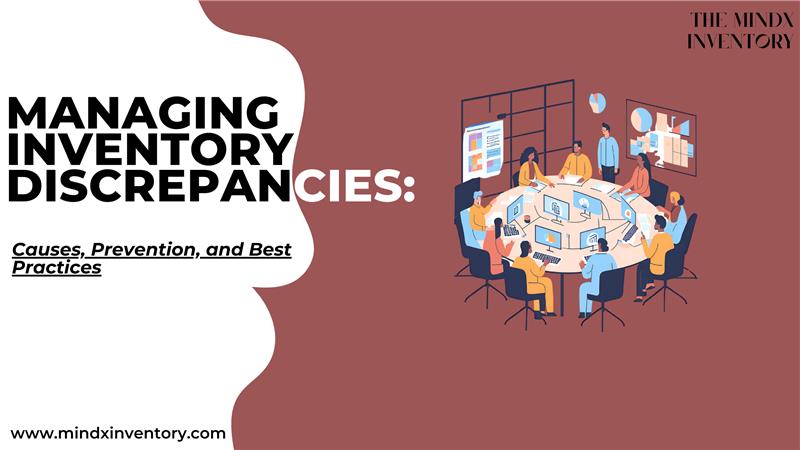
Introduction
Inventory discrepancies can significantly disrupt business operations, lead to financial losses, and result in customer dissatisfaction. Whether you’re facing unexpected surpluses or shortages, it’s crucial to identify the root causes and implement effective preventive measures. In this article, we’ll explore common reasons for inventory mismatches and share best practices for maintaining accurate stock levels using MindX’s advanced inventory management system.
What is an Inventory Discrepancy?
An inventory discrepancy occurs when the recorded stock levels in your system do not match the actual physical inventory. This mismatch can lead to operational inefficiencies, misinformed purchasing decisions, and revenue losses. Discrepancies can manifest in two primary forms:
- Shortages: Fewer items in stock than recorded, which can lead to missed sales opportunities and dissatisfied customers.
- Surpluses: More items in stock than expected, tying up capital and increasing holding costs.
Understanding these discrepancies is essential for maintaining a healthy inventory and ensuring that your business runs smoothly.
Common Causes of Inventory Discrepancies
Inventory discrepancies typically arise from a combination of factors rather than a single cause. Here are some of the most common contributors:
- Human Error: Mistakes in counting, data entry, or stock handling can result in incorrect inventory records. Even the most diligent employees can make errors, especially during busy periods.
- Theft and Fraud: Unauthorized stock removal can lead to inventory shortages and financial losses. Implementing security measures can help mitigate this risk.
- Damage or Spoilage: Unaccounted-for damaged or expired items can distort inventory levels. Regular inspections can help identify and address these issues promptly.
- Vendor Errors: Inaccurate shipments or invoicing issues can cause inventory mismatches. Establishing clear communication with suppliers is vital for resolving these discrepancies.
- System Glitches: Software bugs, data sync issues, or misconfigurations can compromise record accuracy. Regular system maintenance and updates can help prevent these problems.
- Poor Inventory Management: Inefficient stock tracking and lack of clear procedures can contribute to discrepancies. Streamlining processes and implementing best practices can enhance accuracy.
- Natural Disasters: Unexpected events such as fires or floods can lead to sudden stock loss. Having a contingency plan in place can help businesses recover more quickly.
How to Prevent Inventory Discrepancies
Understanding the causes of discrepancies is the first step toward prevention. Here are six essential strategies to minimize inventory mismatches:
Cycle Counting
Instead of conducting full stock audits infrequently, perform regular cycle counts for specific product categories. This practice allows for early detection and correction of discrepancies before they escalate, ensuring that your inventory records remain accurate.
Implement an Inventory Management System
Utilizing a robust inventory management software like MindX Inventory can provide real-time tracking, automate stock updates, and minimize human error. Features like barcode scanning and RFID tracking enhance accuracy and efficiency, making it easier to manage your inventory effectively.
Employee Training
Ensure all employees handling inventory are well-trained in stock management procedures. Clear documentation and standard operating procedures (SOPs) should be available to guide them. Regular training sessions can reinforce best practices and keep staff informed about any updates.
Regular Process Audits
Periodically review and refine inventory management processes, including storage organization, receiving protocols, and picking methods. This helps identify inefficiencies and improve accuracy, allowing your team to work more effectively.
Use Stock Tracking Technology
Barcode scanners and RFID technology enable automated, real-time tracking of inventory movement. This minimizes manual data entry and ensures accurate stock updates, reducing the likelihood of discrepancies.
Vendor Verification
Establish a habit of cross-checking vendor invoices and shipments upon arrival. Maintaining transparent communication with suppliers helps resolve discrepancies quickly and prevents issues from compounding, ensuring that your inventory records remain accurate.
Best Practices to Reduce Inventory Discrepancies
In addition to preventive measures, integrating these best practices into your inventory workflow will further enhance accuracy and efficiency:
Promote a Culture of Accountability: Train employees to follow inventory protocols and encourage responsibility in stock handling. When everyone understands the importance of accurate inventory management, discrepancies are less likely to occur.
Identify Root Causes & Improve Processes: Learn from past discrepancies and adjust processes to prevent recurrence. Conducting post-mortem analyses can provide valuable insights into areas for improvement.
Automate Inventory Tracking: Implement barcode scanning and automated software updates to maintain real-time stock visibility. Automation reduces the risk of human error and streamlines inventory management.
Partner with a 3PL Provider: If managing your own warehouse is overwhelming, consider outsourcing to a third-party logistics provider (3PL) to ensure professional handling of inventory. This can free up resources and allow you to focus on core business activities.
Enhance Your Inventory Management with MindX Inventory.
The best way to eliminate inventory discrepancies is by leveraging modern technology. MindX’s cloud-based inventory management software offers:
- Real-time inventory updates that keep you informed about stock levels at all times.
- Omnichannel inventory tracking to manage stock across multiple sales channels seamlessly.
- Batch and lot tracking for end-to-end traceability, ensuring you know the origin and status of every item.
- Expiry date tracking for perishable items, helping you minimize waste and optimize stock rotation.
- Seamless integration with third-party tools and platforms, allowing for a cohesive operational ecosystem.
Are You Ready to Take Your Inventory Management to the Next Level?
Contact us today for a demo and discover how MindX Inventory can help your business reduce discrepancies and optimize operations! With our innovative solutions, you can take proactive steps to ensure your inventory remains accurate and reliable, ultimately enhancing your overall business performance.
By understanding the causes of inventory discrepancies and implementing effective prevention strategies, businesses can maintain accurate stock levels, enhance operational efficiency, and ultimately improve customer satisfaction. With MindX’s advanced inventory management solutions, you can take proactive steps to ensure your inventory remains accurate and reliable.
Feel free to adjust any sections or add specific features that highlight the unique advantages of MindX!